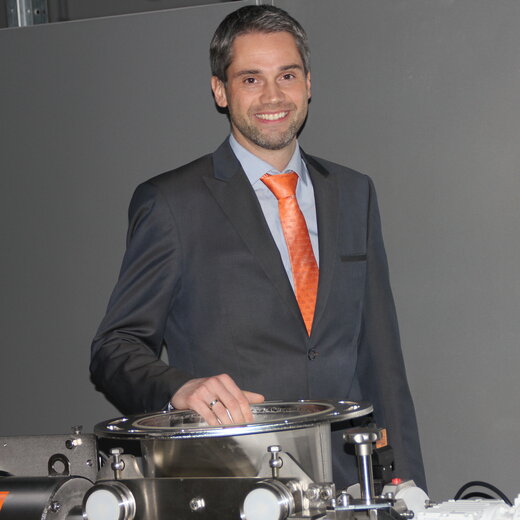
Thierry Peeters
Sales Manager AZO®Poly
Bulk goods handling for compounding different materials (fibre-reinforced) with maximum flexibility and manual premix production