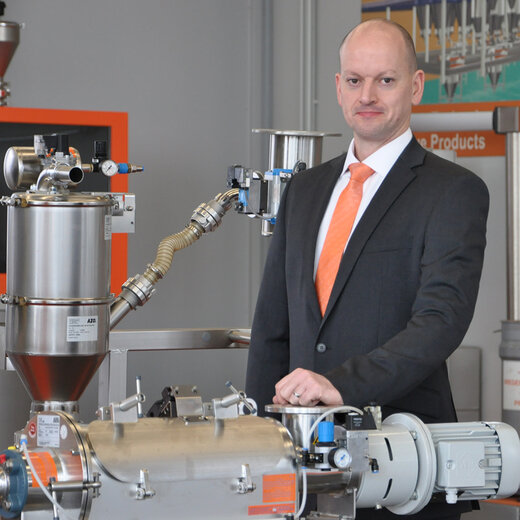
Chris Matthews
Sales Manager
We are experiencing a rethink. Awareness of the finite nature of fossil resources has grown significantly in recent decades, and the increasingly clear signs of climate change and environmental pollution have shown at the latest: We must learn to use our resources sparingly and sustainably. Plastics in particular are criticised in this aspect, as they are mostly made from petroleum and cannot be completely degraded naturally.
For this reason, we at AZO are intensively involved with the topic of recycling and the question of how plastics can be successfully processed and reused without having to accept too great a loss of quality. Upcycling is the keyword – a type of recycling in which reprocessing results in a product that is at least as high quality or higher quality than the original material.Depending on the type of raw material and industry, this results in very specific challenges.
So-called post-consumer recycling often involves polyolefin-based film packaging. These can come in a wide variety of forms and sometimes have widely varying flow properties. Depending on the pre-process, i.e. whether the products have been shredded, ground, washed or sorted, there are different requirements for the raw material automation.
Due to their low bulk density, one of the biggest challenges is the handling of ultra-light film shreds - especially during product feeding. For this problem, we at AZO have developed discharge solutions with agitators, vibratory trays and special geometries to prevent the product from sticking and bridging.
The next step is the discharge from the separator. For this purpose, we have designed appropriate separators that have particularly large outlet cross-sections and are without interfering contours. Together with a pneumatic piston vibrator, even the lightest products can be discharged safely.
Meanwhile, the market for recycled plastics is growing. The Israeli company UBQ, for example, has developed a filler that consists of 100% recycled household waste and can be used in many ways for the production of sustainable plastics.
For this, the filler has to be fed into the manufacturing process of plastics and poses a real challenge for automated handling. This is because UBQTM, or fibrous regrinds in general, exhibit poor flow behaviour and tend to bridge and snag.
Here too, AZO offers suitable discharge systems and feed hoppers to feed the product into the process as safely and efficiently as possible.
In industry, the recycling of one's own production waste is usually already common practice. DEKURA Kunststoffrecycling, however, goes a step further and takes over waste cuttings from window production as well as old windows and roller shutters throughout Europe and processes them. In this way, high-quality secondary raw materials are produced from production waste, which can then be used again in window profile production.
For this purpose, the window waste is shredded, ground and, in several sorting steps, the PVC is separated from glass and fittings and washed. They are then processed into a clean PVC granulate that can be fed into the production of new windows.